Un kit de protection pour imprimante 3D conquiert l'Amérique
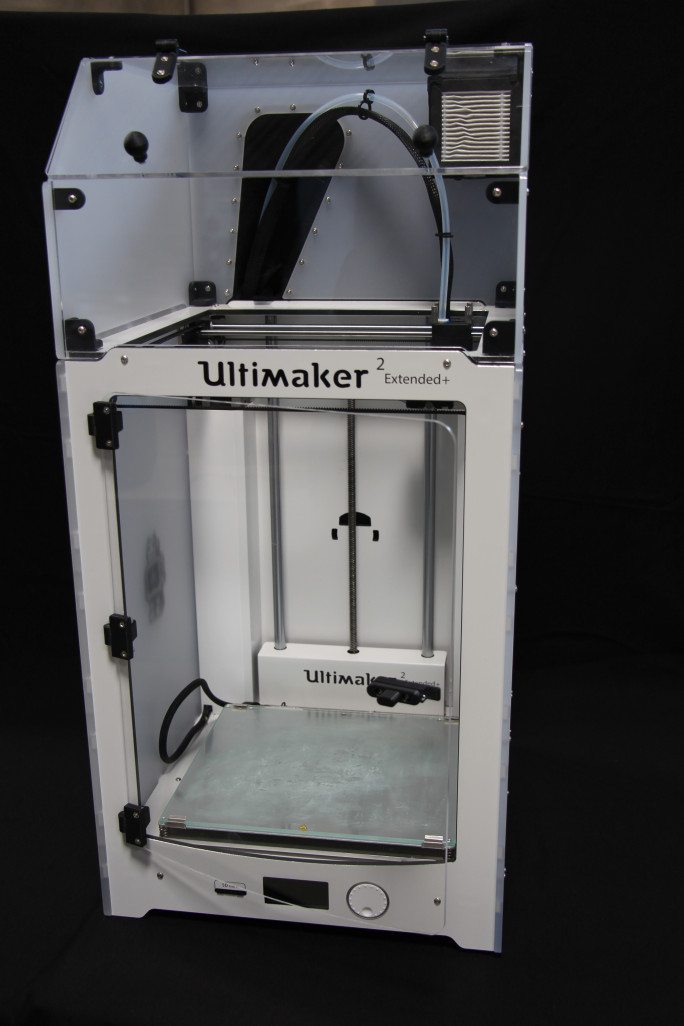
Imaginez un capot en Plexiglas qui se clipse, doté d’une ventilation et d’un filtre à particules, que vous posez simplement sur votre imprimante 3D, qui travaillait jusque-là à l’air libre, et qui immédiatement vous isole du bruit, des particules toxiques et qui, de surcroît, évite le fameux “warping”, une déformation de la pièce due à un choc thermique. C’est cette trouvaille pratico-pratique – le capot Ultimaker − que viennent de mettre au point deux Boulonnais et qui commence à fleurir sur tous les sites professionnels de vente en ligne d’imprimantes 3D. Plus de 200 pièces viennent d’être livrées aux Etats-Unis.
Suite à un “Arduino Day” organisé au Fablab de Calais-Côte d’Opale en mars 2015 (Arduino étant une petite carte électronique programmable combinée à un logiciel multiplateforme, dans le but de créer facilement des systèmes électroniques), deux Boulonnais, Stéphane Watré et François Damay, découvrent les secrets de la programmation. Ils deviennent des passionnés du développement de projets. “Surtout François, concède Stéphane Watré. C’est un passionné, un ‘maker’. Il développe des solutions. Il existe une forte communauté sur Internet, où l’on partage ses réalisations.” Ils décident d’acheter une première imprimante 3D semi-professionnelle. Très vite, le problème du warping devient un handicap dans la réalisation des pièces. “J’ai mis un plastique sur l’imprimante et ça marchait mieux, explique Stéphane Watré, mais ce n’était pas encore idéal.” Ils se rendent un samedi au FabLab Côte d’Opale, découpent des plaques en Plexiglas qu’ils assemblent avec des pièces en plastique, fabriquées par leur imprimante… Très vite, le capot Ultimaker devient la coqueluche des salons professionnels.
Haro sur les particules toxiques. Mais l’aventure ne s’arrête pas là. Des études scientifiques commencent à pointer du doigt les émissions de particules fines et et de composés organiques volatiles liées aux imprimantes 3D. Représenteraient-t-elles un risque pour notre santé ? Oui, répondent des chercheurs l’Institut de technologie de l’Illinois et de l’École des ingénieurs de la ville de Paris, qui ont publié une étude dans la revue Environmental Science & Technology. Suite à des test réalisés, l’analyse a permis de relever des quantités plus ou moins importantes de particules ultrafines, d’une taille inférieure à 100 nanomètres, appelées également nanoparticules, et potentiellement dangereuses pour les personnes atteintes de troubles respiratoires. L’étude conclut avec quelques recommandations pour les fabricants, comme le développement de nouveaux filaments d’impression aux émissions réduites de particules ou l’installation de filtres à air. Les auteurs rappellent également d’utiliser les imprimantes 3D dans des espaces ventilés, surtout dans les écoles ou tout site de formation.
Les salons professionnels boostent les ventes. Dès lors, Stéphane Watré et François Damay, conçoivent un boîtier avec un ventilateur et un filtre à particule qu’ils insèrent dans le kit de protection. Ils constatent qu’au bout d’une semaine d’utilisation, le filtre est noir. Dès le mois de novembre 2015, ils commencent à fabriquer une trentaine de capots par mois. L’entreprise Machines-3D les invite à participer au salon 3D Print Show, qui se tenait pour la dernière fois à Paris en octobre dernier. Le leader de l’impression 3D, Makershop 3D, vient les voir sur leur stand, est séduit par le produit et leur donne l’aval pour commercialiser leur capot sur l’ensemble du monde. Les commandes affluent des Etats-Unis, à destination principalement des institutions et des écoles. Cinq imprimantes 3D fonctionnent 24 heures sur 24 pour répondre à la demande. “Avec ce mode de production, nous pouvons aller jusqu’à 150 capots par mois, explique Stéphane Watré. Au-delà, nous envisagerons le procédé à injection.“
Les deux hommes ne s’arrêteront pas là. Ils ont entamé un partenariat avec l’Ecole d’ingénieurs du Littoral Côte d’Opale, et notamment deux élèves ingénieurs en informatique, pour travailler sur la réalisation d’une application intégrée au capot. L’idée est de connecter le capot à Internet…
Selon les dernières prévisions de l’institut américain Gartner, connu pour sa courbe annuelle des tendances high-tech, le nombre d’imprimantes 3D vendues pour l’année 2016 devrait se rapprocher de la barre symbolique du demi-million d’unités dans le monde, soit une hausse de près de 103% par rapport à 2015. De quoi envisager très vite le procédé à injection !
Lucy DULUC