Trois projets innovants labellisés en cours...
Début juillet, dans le Valenciennois, lors d’une journée consacrée à l’innovation dans le matériel roulant, des exemples ont été présentés. Domaines concernés : interventions de maintenance, détection et prévention des pannes, utilisation de matériaux composites…
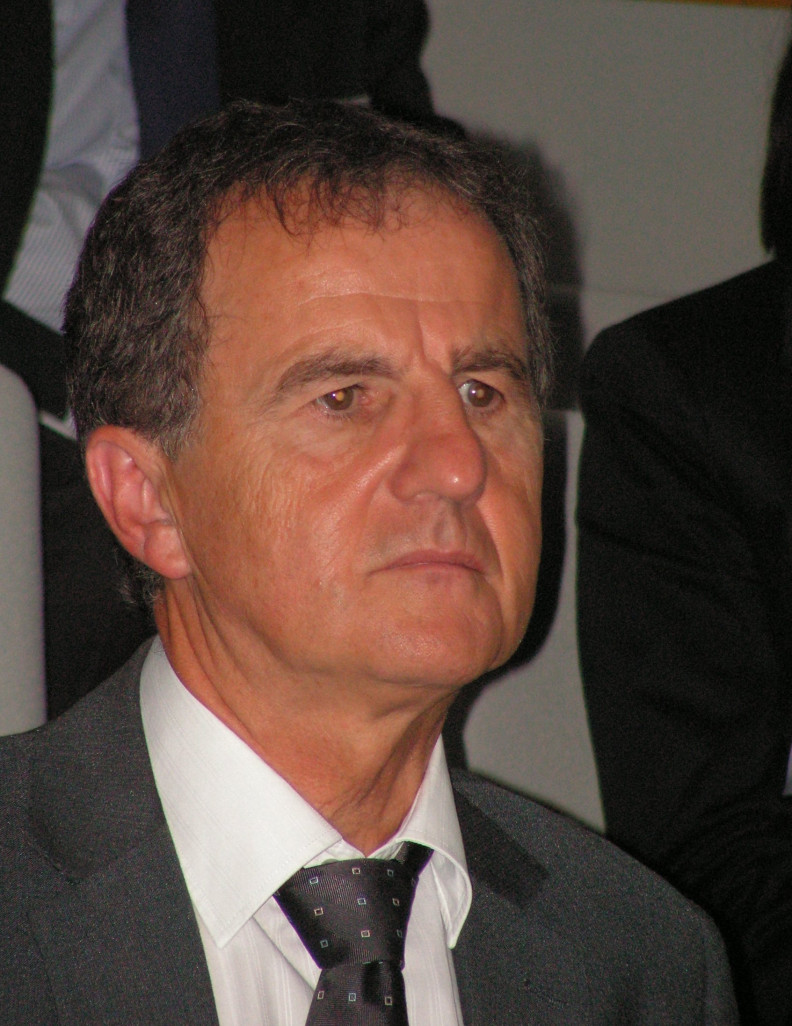
Ce pôle de compétitivité, baptisé i-Trans, a été créé en 2005. Sa vocation est d’apporter un soutien à l’innovation, par l’accompagnement de projets, concernant les mondes de l’industrie, de la recherche et de la formation dans le transport terrestre, l’automobile et le ferroviaire en l’occurrence, bien représentés dans le Hainaut. Le 3 juillet dernier, dans les locaux du CISIT (Campus international sur la sécurité et l’intermodalité dans les transports), premier bâtiment du futur technopole Transalley au sud de Valenciennes, s’est déroulée une deuxième journée de l’innovation. La première ayant eu lieu à Eurotunnel sur le thème des infrastructures ferroviaires. Là, début juillet, dans l’amphi du CISIT, sur grand écran, devant une centaine de personnes, les trois projets d’innovations concernaient le matériel ferroviaire roulant et 16 partenaires, entreprises et laboratoires. Tous trois sont labellisés «i-Trans».
En voici une présentation rapide. Ces projets à vocation internationale usent volontiers des anglicismes.
W3M (Wheel Mobile Milling Machine). Ce projet, porté par l’entreprise de Lys-lez-Lannoy Sogema engineering (conception et réalisation d’équipements d’ateliers ferroviaires), a été présenté par Frédéric Guillot. But : réduire les temps de dépannage résultant d’incidents de freinage, fréquemment constatés sur les wagons de fret de la SNCF et de la SNCB. Des visites de maintenance, a-t-il dit, ont montré que des roues étaient endommagées du fait du mauvais fonctionnement des freins. L’intervenant a expliqué que ces incidents avaient pour effets des encombrements de voies, le déclenchement de moyens lourds et coûteux, des interventions d’usinage pénibles pour les opérateurs.
W3M, a-t-il dit, doit réduire le temps d’immobilisation et de dépannage (4 heures pour deux essieux endommagés) par l’utilisation de moyens d’intervention plus légers et efficaces. Ainsi, après intervention, soit la capacité de circulation est rétablie, soit le convoi peut rejoindre l’atelier de maintenance le plus proche.
W3M signifie «roue fraiseuse portable» et permet d’éviter l’enlèvement du wagon ou le changement de bogies sur les voies. L’intervention se réalise au moyen d’une machine d’usinage installée sous les roues.
Où en est ce projet ? Démarré en 2010, il représente un investissement de 250 000 euros. Un étudiant de l’ENSAM y a participé. Le brevet a été déposé. Un prototype a été réalisé. Une deuxième phase de développement a commencé. Des financements sont recherchés.
SURFER (un). Le nom complet est «Surveillance ferroviaire active pour la détection et le diagnostic embarqué de pannes». Il a été présenté par Guillaume Branger, de chez Bombardier, entreprise initiatrice du projet. En tout, trois industriels et deux labos sont concernés. Il s’agit à terme, par un système de maintenance (embarqué dans le meilleur des cas), d’anticiper sur les pannes et de réduire de 30% les temps d’intervention. Domaine concerné pour l’instant : les systèmes d’ouverture et de fermeture des portes et des emmarchements de trains. Par la suite, SURFER pourrait s’appliquer aux pantographes, batteries, compresseurs, équipements électroniques, freinage.
L’intervenant a énuméré les difficultés à surmonter : coordonner les liaisons «sol/bord», intégrer le nouveau système de capteurs servant à la prédiction aux calculateurs existants, concilier ce qui relève de la maintenance et de la sécurité… M. Branger a dit qu’il y avait des «verrous technologiques» à faire sauter…
L’expression est souvent revenue dans les exposés.
Où en est ce projet ? Initié en 2010, il représente un investissement de 3 millions, soutenu par l’Etat, les conseils régionaux Nord-Pas-de-Calais et Ile de France, et le FEDER. Pour l’instant, il n’est pas entièrement «embarqué» et sa validation est en cours sur une mini-flotte du Francilien de la SNCF. C’est là, a dit l’intervenant, que le système va faire ses preuves. Les applications industrielles sont espérées pour 2020.
SURFER (deux). Sur le même projet est intervenu Frédéric Grzesiak, directeur technique au sein de la société Prosyst (Templemars), une SAS filiale d’un éditeur français de logiciels électriques. Il a expliqué que sa société, créée à Valenciennes en 1986, n’était pas présente dans le ferroviaire avant ce projet, son domaine étant celui de l’automobile. Il a précisé que Prosyst considérait le train comme une «usine qui roule» avec ses systèmes et son organisation humaine.
L’objectif est, en gros, de transposer au train une technologie appliquée à l’automobile (dans le domaine du hardware et du software) et d’imaginer, comme il a dit, des «produits et des stratégies» capables de résoudre les problèmes de surveillance et de diagnostic, de transmission des informations, de ne pas limiter les solutions à un seul train mais de l’étendre à l’ensemble d’une flotte. M. Grzesiak a expliqué qu’il était très confiant «dans ce marché à forte demande». Il a ajouté qu’en tant que fournisseur de Bombardier, Prosyst serait liée à Bombardier pendant cinq ans à partir de la date de commercialisation…
Où en est ce projet ? Frédéric Grzesiak a expliqué que l’homologation était en cours, tout comme des discussions avec la SNCF, incontournable donneur d’ordre (notamment sur la question de la cohabitation entre les nouveaux systèmes et les calculateurs existants).
ULTIMAT. Ce projet, qui signifie «Utilisation innovante de nouveaux matériaux», a été présenté par Emigliano Campus, d’Alstom. Il concerne l’utilisation de matériaux dits composites, autre que l’acier et l’alu, dans la fabrication des caisses de voitures pour voyageurs, soit dans l’urbain, soit dans le TGV. Par matériaux composites, il faut entendre, par exemple, le verre et le carbone. Le côté innovant vient aussi du fait que le ferroviaire reste attaché à une tradition métallurgique, à la différence de l’automobile ou de l’aéronautique.
Les enjeux et difficultés à surmonter du projet Ultimatsont multiples : gagner du poids, ce qui permettrait de réduire la masse des essieux et d’intégrer des équipements nouveaux sans augmenter la charge utile ; réduire le nombre de pièces ainsi que les temps d’intégration et de fabrication ; réaliser des économies d’énergie ; réduire les coûts à l’achat et au recyclage car les composites reviennent plus cher… A résoudre également, étant donné qu’il y a des passagers, les problèmes d’isolation acoustique nés de l’existence d’une structure intérieure et extérieure.
Où en est le projet ? La validation industrielle et mécanique a été faite, mais uniquement pour des prototypes. Les tests en ligne n’ont pas encore été réalisés et l’établissement des normes est en cours. Les tests se feraient avec un wagon intercalé dans un train en service. Là encore, il y aura des «verrous technologiques» à faire sauter et une étude inédite sur le comportement des nouvelles pièces….
Ce projet, initié en 2007 par Alstom transport qui y travaille depuis 1996, concerne sept partenaires et représente un investissement de 11 millions.