Economie circulaire autour des poussières d'acier
L’entreprise, spécialisée dans le recyclage des résidus de poussières d’aciérie, a organisé deux journées portes ouvertes, à l’occasion de la Semaine de la chimie. L’occasion pour les riverains de découvrir le process assez spectaculaire d’une entreprise qui tourne de nouveau à plein régime.
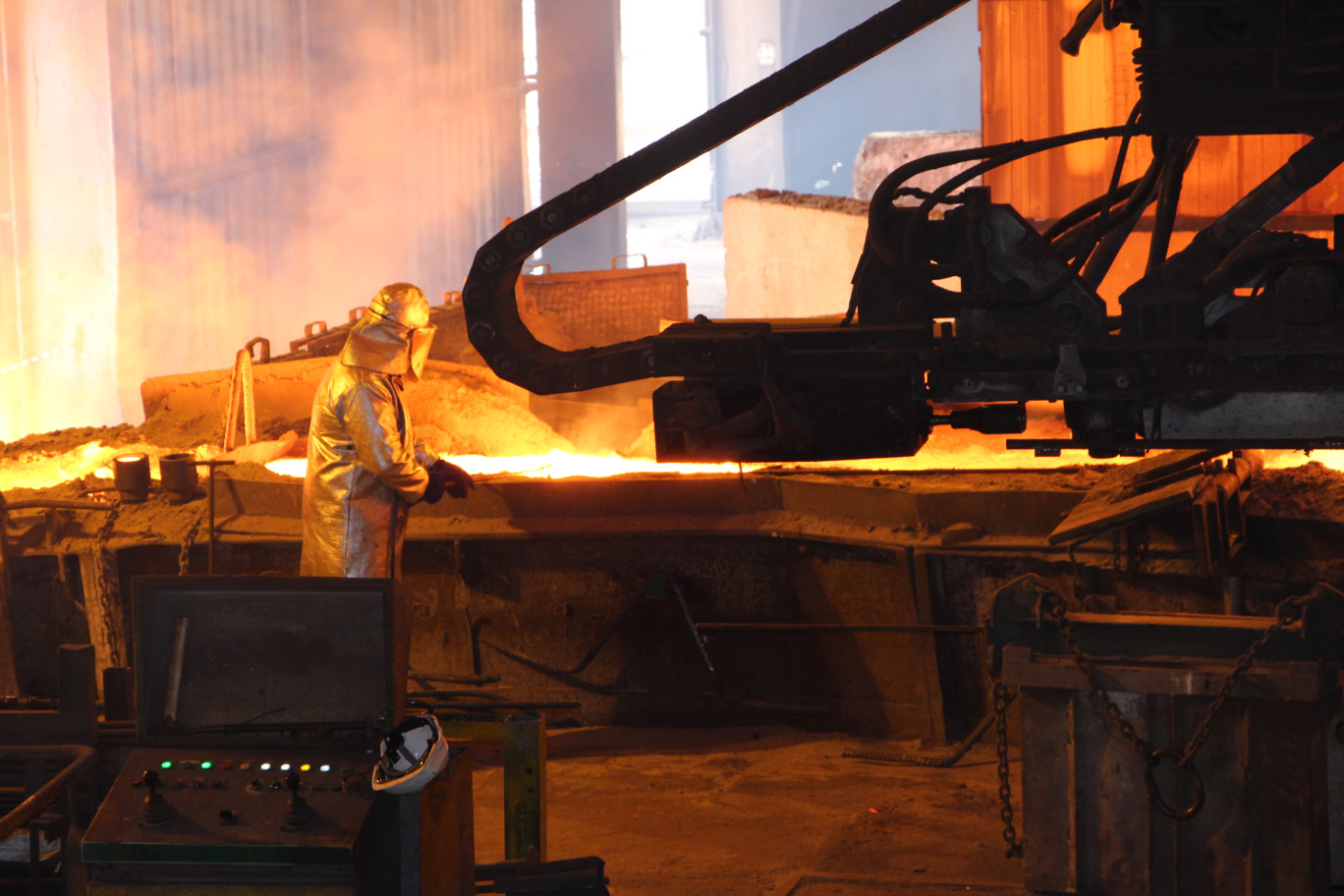
Le métal en fusion est toujours un spectacle impressionnant. C’est ce que les riverains et les entreprises voisines de Befesa (du groupe européen Befesa Valera, espagnol d’origine mais racheté en 2013 par un fonds d’investissement allemand et désormais coté à la Bourse de Francfort) ont pu constater lors des journées portes ouvertes.
L’entreprise, située à Gravelines, est spécialisée dans le recyclage des résidus de poussières d’aciérie. Après avoir subi de plein fouet la crise, le site tourne de nouveau à plein régime, porté par la forte hausse de la production d’acier. «Nous recyclons la poussière d’acier inoxydable, riche en chrome et en nickel, envoyée par nos clients sidérurgistes. Il faut savoir que la production d’une tonne d’acier génère 30 kg de poussières. Nous l’extrayons sous forme d’un ferroalliage (fer, chrome et nickel). Celui-ci repart ensuite chez ces mêmes clients, puisque c’est une très bonne matière première pour la fabrication de l’acier. Nous sommes donc complètement dans une économie circulaire», détaille Denis Chevé, directeur du site.
Befesa traite chaque année 65 000 tonnes de résidus pour une production de 35 000 tonnes de ferroalliage. Ces clients viennent surtout de Belgique, d’Allemagne, d’Espagne et de Scandinavie. Ce sont 80 personnes qui travaillent sur le site gravelinois de Befesa dont le process consiste à agglomérer les poussières réceptionnées en briquettes, ensuite placées dans un four électrique afin de les faire fondre pour récupérer le nickel et le chrome. Chez Befesa, rien ne se perd puisque le laitier, sous-produit issu de la fusion, sera récupéré lui aussi et utilisé comme remblais par des entreprises du BTP. Quant aux poussières issues du process, riches en zinc, elles seront lavées et retraitées en interne via un autre site du groupe, Befesa Zinc, pour en faire de l’oxyde de Waelz. Un four, sur les deux que compte le site, tourne actuellement à plein régime. «Mais si la tendance se poursuit, il n’est pas impossible que nous remettions en route notre second four», précise Denis Chevé, dont l’une des préoccupations quotidiennes est le prix de l’électricité, qui représente 30% du coût de fabrication du ferroalliage. «A l’avenir, il nous faudra aussi, sans doute, penser notre consommation différemment et nous adapter à l’augmentation de la part des énergies renouvelables dans la production d’électricité en devenant des ‘flexiconsommateurs’. C’est notre modèle qu’il faut complètement revoir et c’est dès à présent que nous nous y penchons», conclut-il.