Daher mise sur les thermoplastiques pour décarboner l'avion
Du thermoplastique pour décarboner l'aviation? C'est le choix de Daher, un des plus anciens groupes industriels familiaux français, qui développe des solutions pour l'avion de demain, y compris comment le...
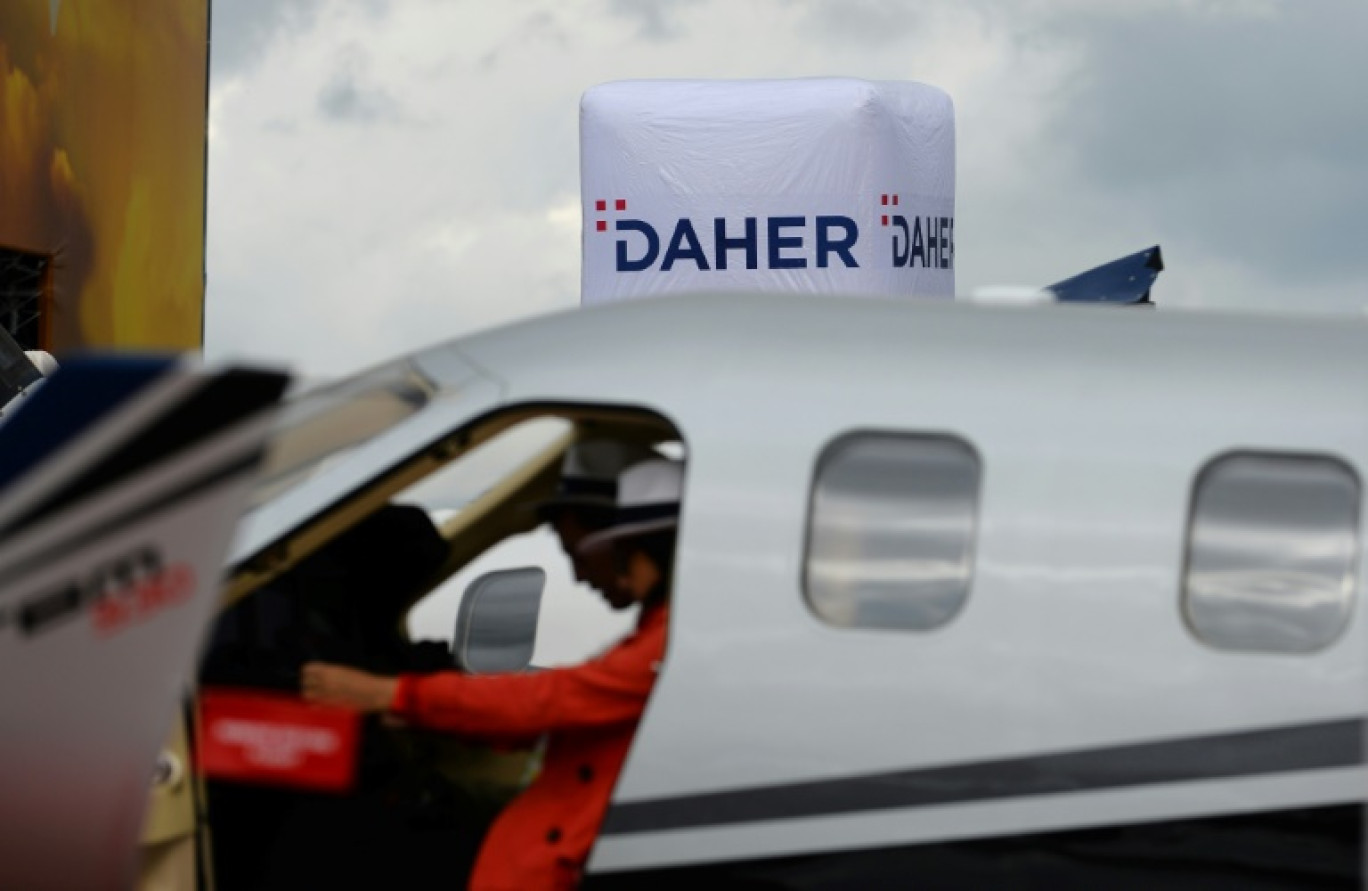
Du thermoplastique pour décarboner l'aviation? C'est le choix de Daher, un des plus anciens groupes industriels familiaux français, qui développe des solutions pour l'avion de demain, y compris comment le recycler en fin de vie.
Même si cela peut sembler contre-intuitif, les thermoplastiques, composés de fibres de carbone très légères et très rigides et de liant en résine plastique, sont déterminants de point de vue du développement durable: ils permettent d'alléger l'avion qui consomme ainsi moins de carburant et présentent d'autres avantages en termes de résistance et de recyclabilité.
Chez Daher, ce matériau est notamment testé pour fabriquer les nervures, des pièces critiques qui rigidifient l'aile, comme les côtes dans le corps humain, et supportent jusqu'à 30 tonnes.
Au centre d'innovation de Saint-Aignan-de-Grandlieu, près de Nantes dans l'ouest de la France, interdiction de prendre des photos, mais on peut soulever ces pièces, version aluminium et version thermoplastique, pour comparer leur poids.
"On gagne 20-25% en masse sur le même produit, avec la même résistance mécanique", souligne Dominique Bailly, directeur recherche et développement de Daher.
Ces pièces intégreront l'"aile de demain" - longue, fine et légère censée améliorer l'aérodynamique de l'avion, présentée fin mars au Airbus Summit du géant européen, qui est client de Daher tout comme son concurrent américain Boeing.
"On montrera notre maturité technologique lorsque les appels d'offres pour l'avion de demain tomberont, à la fin de la décennie", déclare Dominique Bailly à l'AFP.
- Oeuf et tablette de chocolat -
Les propriétés des matériaux thermoplastiques offrent des perspectives intéressantes. "On transforme la matière en cinq minutes au lieu de huit heures pour les composites thermodurcissables", souligne Dominique Bailly, ce qui permet de s'adapter aux cadences "fulgurantes" dans l'aéronautique.
Contrairement aux thermodurcissables largement utilisés aujourd'hui, dont la transformation est irréversible, le thermoplastique devient mou ou liquide quand on le chauffe et se solidifie en refroidissant - des cycles qui peuvent se répéter presque à l'infini.
Comme une tablette de chocolat, à l'inverse d'un oeuf qui ne redeviendra pas liquide une fois cuit.
De plus, les thermoplastiques se conservent à température ambiante tandis que les thermodurcissables se gardent dans des congélateurs consommant beaucoup d'énergie.
"Le thermoplastique va pouvoir être soudé avec des procédés d'induction ce qui permet de remplacer aujourd'hui la jonction réalisée avec des boulons ou des vis, très lourds", explique à l'AFP Julie de Cevins, directrice développement durable de Daher.
Cette soudure mise au point par Daher avec le spécialiste néerlandais KVE, racheté en 2019, permet une réduction de poids des aérostructures - les pièces principales d'un avion - allant jusqu'à 15%.
- Pédales en composite recyclé -
Le démonstrateur de plan horizontal fixe, pièce critique à l'arrière de l'avion qui assure sa stabilité en vol, a été validé fin 2024, confirmant sa faisabilité industrielle.
"On commence à utiliser des composites aussi dans les zones tièdes des moteurs en remplaçant celles en titane", souligne auprès de l'AFP Pierre Rouch, expert en thermoplastiques.
Un gain en souveraineté, sachant que le titane vient principalement de Russie.
Les thermoplastiques ne peuvent pas tout remplacer, mais leur part va progressivement augmenter dans les avions de prochaine génération, résume Dominique Bailly.
Quant aux chutes de thermoplastiques, elles sont broyées, cisaillées, puis transformées en granulés. Deux tonnes ont déjà pu ainsi être réutilisées chez Daher.
"Il n'y a aucune matière qui a été ajoutée pour obtenir le granulé, pas de résine neuve, pas d'additifs. On est 100% circulaire et on retrouve les mêmes propriétés physico-chimiques sur le sous-produit", souligne Julie Dausseins, spécialiste du recyclage.
Ce procédé a été appliqué pour remplacer les pédales de pilotage de l'avion TBM de Daher, traditionnellement en aluminium. Validées par les autorités européennes, elles seront intégrées en série cette année.
Avec cette technologie, Daher vise des marchés hors aéronautique dans le médical, le sport et les loisirs. La société est notamment en contact avec des orthopédistes, intéressés par ce procédé pour la fabrication d'orthèses au niveau de la jambe, résistant à l'eau et au sable sur la plage.
39PD7KD