Novares, un acteur incontournable de l’injection plastique automobile
Présent dans un véhicule sur trois à travers le monde, le groupe développe et fabrique des pièces plastiques sur-mesure pour les plus grands noms de l’automobile. Ses sites de Lens et Libercourt jouent un rôle clé dans cette organisation internationale.
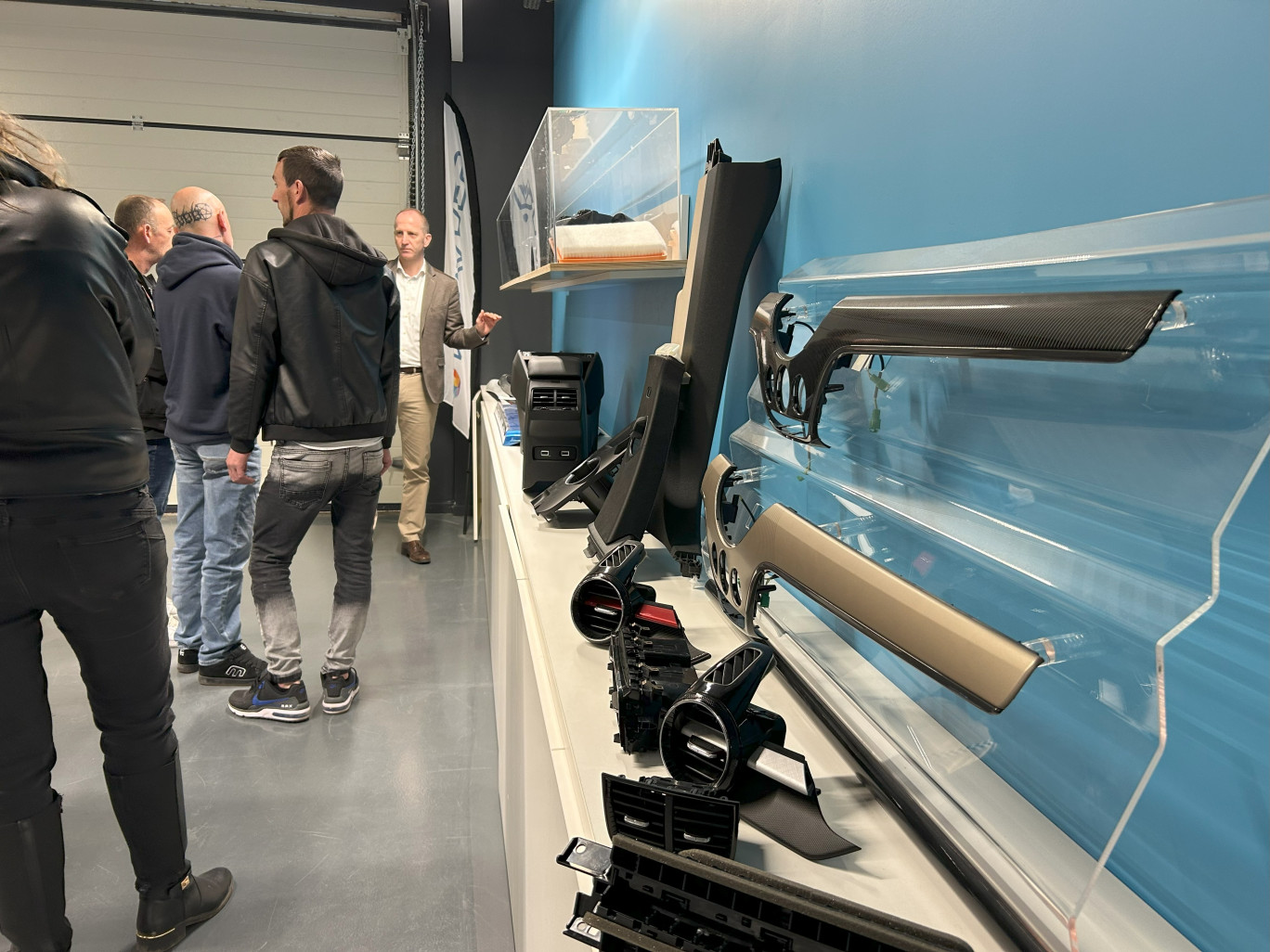
«L’injection plastique, c’est notre cœur de métier», résume Luc Dornier, chief product development officer au sein de Novares. Avec un chiffre d’affaires de 1,4 milliard d’euros et 8 300 collaborateurs répartis dans 37 usines, 6 skill centers et 7 technical centers, le groupe est solidement implanté à l’échelle mondiale.
Boîtes à gants, poignées, grilles d’aération, pièces moteur… La diversité des produits réalisés est vaste. «Nous fabriquons à la demande, en étroite collaboration avec nos clients. Il n’existe pas de catalogue chez nous», précise Luc Dornier. Stellantis, Toyota, Ford, Mercedes, Renault, Dacia… les plus grands constructeurs font appel à son savoir-faire.
Un site logistique sous haute cadence
En Europe, c’est principalement l’usine de Libercourt qui alimente les clients de l’entreprise. Le site emploie 300 salariés et fait preuve d’une cadence impressionnante. «Entre 45 000 et 50 000 pièces sortent chaque jour de cette usine», chiffre Luc Dornier. L’entreprise fonctionne en flux tendu : les pièces fabriquées le matin sont, pour la plupart, expédiées en camion dès la fin de l'après-midi. «Un camion vient charger environ toutes les 45 minutes. À l’année, cela représente 7 500 camions, soit 32 camions par jour», précise Frédéric Niels, directeur de l’usine.
Dans les ateliers, impossible de rater les presses d’injection allant de 140 à 2 300 tonnes. Une pièce est fabriquée ici en seulement 70 secondes, afin de suivre les cadences imposées par les constructeurs automobiles. «Nos moules aussi sont massifs : ils pèsent plusieurs tonnes», ajoute Frédéric Niels. «Notre production est ultra-précise. Comme nous travaillons à flux tendu, nous n’avons pas droit à l’erreur». Un changement de moule - et donc de série de production - demande 45 minutes. Un exercice que les équipes maîtrisent parfaitement : elles en réalisent 4 700 chaque année. «Nous devons avoir les yeux rivés en permanence sur nos commandes, pour ne rien oublier et effectuer les changements au bon moment», conclut le directeur.
Imaginer les pièces plastiques de demain
Avant d’être produites, les pièces sont d'abord développées dans les skill centers du groupe, comme celui de Lens. «Depuis 1991, 130 personnes travaillent ici, se réjouit Luc Dornier. Notre mission est claire : transformer les idées en prototypes, imaginer les pièces plastiques de demain et accompagner les mutations de l’automobile». À Lens, chercheurs et ingénieurs ne se contentent pas de répondre aux demandes des clients ; ils innovent également. «Il faut toujours avoir un coup d’avance. Il y a trente ans, notre objectif était de transformer les pièces métalliques des moteurs en pièces à injection plastique. Peu à peu, nous y sommes parvenus», explique Luc Dornier. Il faut dire que les pièces en plastique ont de nombreux avantages. Plus plus légères, elles réduisent les émissions de dioxyde de carbone des véhicules, et elles sont également moitié moins coûteuses.
Aujourd'hui, Novares se concentre sur la production de pièces pour les moteurs électriques et à hydrogène, technologies auxquelles les constructeurs automobiles se tournent de plus en plus. «C'est un véritable défi, car dans un moteur électrique, par exemple, 99% des pièces sont encore en métal», précise-t-il. Les équipes du skill center cherchent à éviter la montée en chaleur et la conductivité des pièces. «C'est pourquoi nous développons des pièces hybrides en plastique et aluminium, et que nous testons des plastiques recouverts de peinture métallisée», témoigne Luc Dornier.
Lens et Libercourt, un duo gagnant
Un showroom installé sur le site permet aux clients de visualiser les dernières innovations. «Certains veulent miser sur le design, d’autres sur la performance technique. À nous de nous adapter», conclut Luc Dornier. Au final, les deux sites forment un binôme stratégique pour Novares. Lens conçoit, Libercourt fabrique. Un modèle efficace qui permet au groupe d’être réactif dans un secteur automobile en pleine mutation.
Simulation et impression 3D pour des pièces parfaites
Au sein du skill center de Lens, les algorithmes et l'impression 3D sont des outils régulièrement utilisés. Ces technologies permettent de tester les prototypes avant même leur fabrication et d’éviter l’utilisation de machines coûteuses. L’objectif est de ne pas produire une pièce susceptible de représenter un investissement important sans être sûr qu’elle répondra aux exigences du cahier des charges du client. Ainsi, chaque pièce est d’abord soumise à des simulations, puis à des tests en laboratoire une fois produite. Si celle-ci révèle que la pièce ne respecte pas les critères requis, des ajustements peuvent être effectués directement sur le logiciel avant un nouveau test virtuel. L’enjeu : que la pièce qui sort des chaînes de production soit immédiatement conforme.