Rencontre avec Philippe Demarez, directeur de Nexans à Lens
«Notre ambition est d’électrifier le futur»
Elle fond 165 000 des 250 000 tonnes de cuivre importées chaque année dans l’Hexagone pour produire des câbles électriques. Immersion au coeur de l’usine Nexans de Lens, avec son directeur, Philippe Demarez.
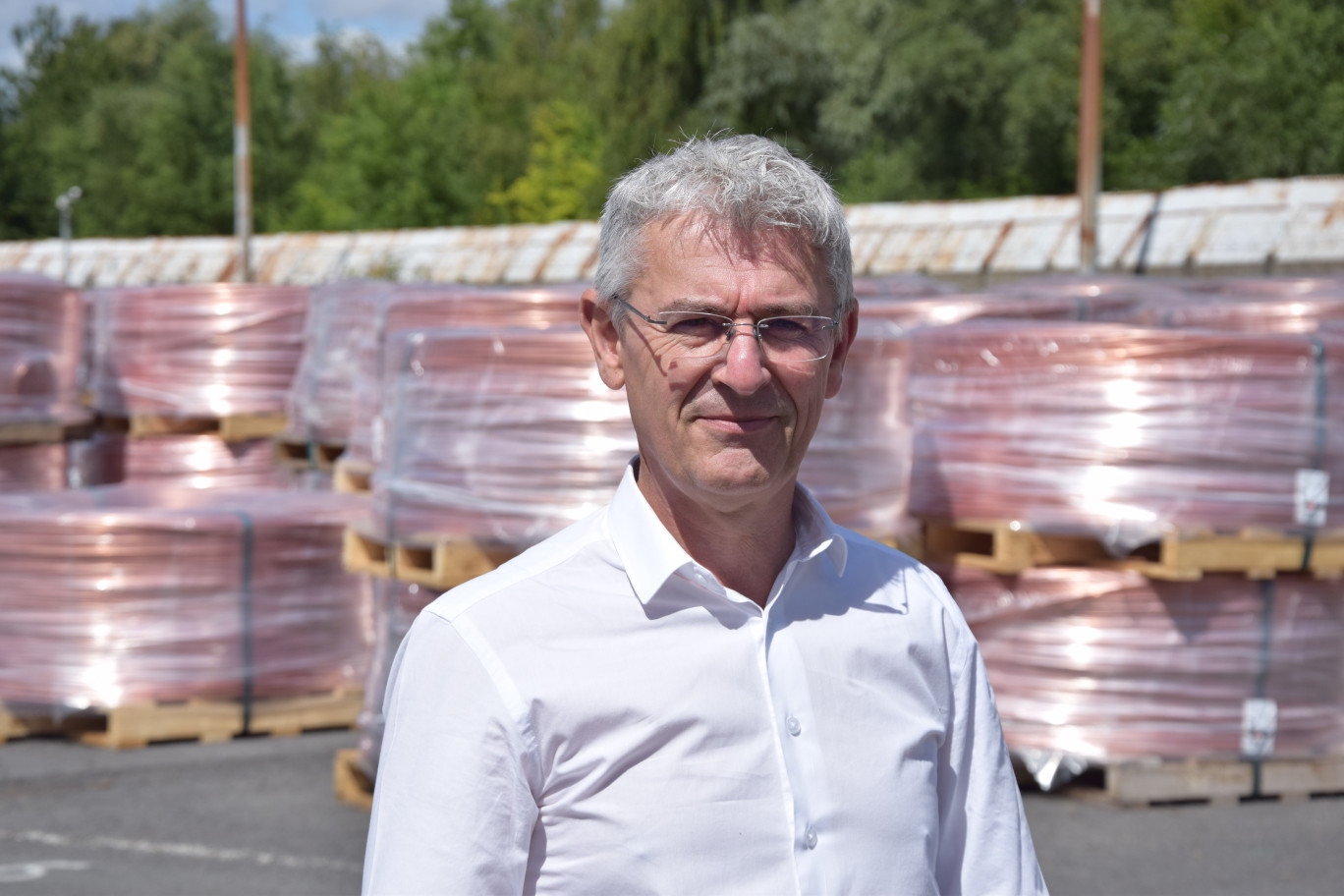
L’histoire débute en 1855 avec la fabrication de cordes en chanvre. Entièrement détruite au cours de la Première Guerre mondiale, l’usine est reconstruite pour démarrer la production de câbles en acier qui serviront, notamment, à la fabrication du pont de Tancarville à la fin des années 1950. En 1921, ses dirigeants ouvrent le premier atelier de tréfilage de métal (étiré en fil) pour la production de câbles électriques et se dotent en 1970 d’une fonderie de cuivre.
Un paquebot de croisière par jour
Désormais, le site de Lens est l’un des maillons forts du groupe Nexans. La production de câbles en acier a été abandonnée au profit de la production de conducteurs en cuivre : une bobine de 5 tonnes sort de l’usine toutes les 8 minutes, soit 700 tonnes par jour (de quoi électrifier un paquebot de croisière) et 165 000 tonnes par an, pour 170 salariés. Les câbles de Nexans électrifient aussi bien les bâtiments que les voitures et les avions, et sont destinés aux projets haute tension acheminant l'électricité entre villes et pays, notamment pour la fabrication de câbles sous-marins.
«Notre ambition est d’électrifier le futur, précise Philippe Demarez. Et depuis une année, l’objectif stratégique est de croître sur les marchés du bâtiment (42% du chiffre d’affaires) et de la haute tension. Sur les marchés des télécoms et de l’industrie, nous subissons la concurrence d’acteurs chinois. Nous ne pouvons pas suivre leurs capacités d’investissement sur tous les marchés, c’est pourquoi nous ne souhaitons pas rester un acteur généraliste mais nous spécialiser sur l’électrification.»
L’usine lensoise est aujourd’hui «la seule fonderie de cuivre pur en France». Ses neuf machines de tréfilage «font chacune le tour du monde chaque jour». Concrètement, la fonderie sort des barres de 8 millimètres affinée jusqu’à 0,2 millimètre dans l’atelier de tréfilage, des câbles qui sont ensuite embobinés sur des tourets. Et «5 M€ d’investissements ont été réalisés au cours des trois dernières années, pour une croissance de 50% des volumes de production», précise le directeur de l’usine.
30% de matières premières recyclées d’ici 2025
Prochainement, la capacité de production devrait encore croître grâce au remplacement du four au sein de la fonderie. «Il date des années 1970 et a été conçu à l’époque pour une capacité de production de 15 tonnes par heure… Nous sommes aujourd’hui à 30 tonnes par heure, les brûleurs fonctionnent à leur maximum. Le projet est en bonne voie et un bâtiment est disponible pour accueillir un nouveau four, donc il n’y aura pas d’arrêt de la production.» La neutralité carbone en ligne de mire, le site mise également sur le triage et le recyclage des déchets de production.
Et face à la croissance constante du cours du cuivre et aux problématiques financières et écologiques liées aux extractions minières, Nexans souhaite développer des «mines urbaines», et passer ainsi de 6% à 30% de matières premières recyclées d’ici 2025. Pour cela, un partenariat avec le groupe Suez lui permet de s’approvisionner auprès de ses centres de tri. Mais selon Philippe Demarez, le manque de capacité de triage en France ne permet pas à l’heure d’actuelle plus de 40% de matières premières recyclées. A suivre…