L’art de la gestion pour une meilleure efficacité
Devant faire face à la concurrence mais aussi à diverses pressions de marchés, les dirigeants doivent trouver le mode de management adapté à leurs organisations, clients et collaborateurs. Objectifs affichés : accroître la valeur créée pour le client et améliorer les performances de l’entreprise tout en prenant en compte les besoins des collaborateurs. Des résultats qui peuvent être atteints en adoptant le Lean Management.
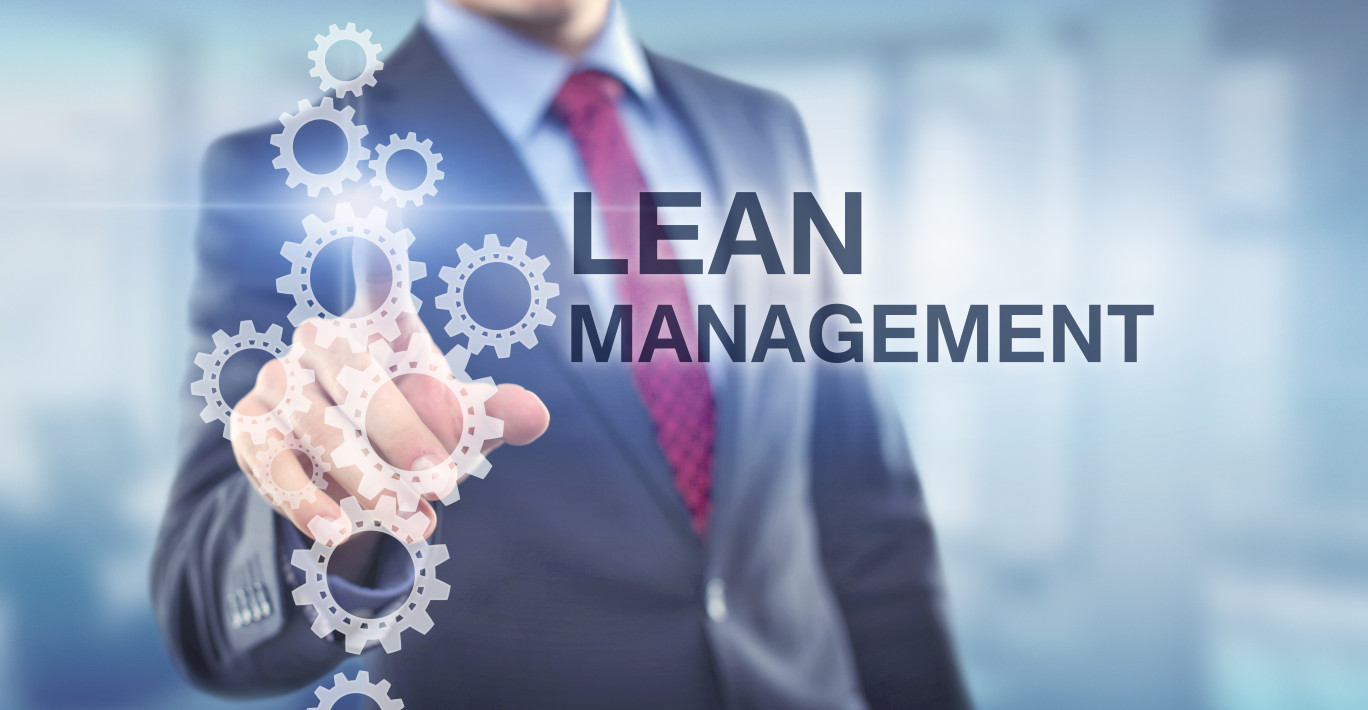
Tirant ses origines du système de production mis en place par Toyota, système de production performant devenu référence dans la gestion de production, le Lean Management couvre aujourd’hui toutes les fonctions support à la production (maintenance, méthodes, approvisionnements) mais aussi les fonctions tertiaires industrielles comme la R&D, le développement et l’industrialisation des produits, les achats… Le champ d’application de ce mode de gestion comprend également le domaine des services ainsi que toutes les fonctions support, notamment les RH, la finance, les services généraux, et les fonctions commerciales y compris le marketing, les ventes, les plateformes d’appels…
Quels en sont les fondements ?
Ayant pour objectif d’améliorer la performance de l’organisation afin de créer de la valeur pour le client tout en prenant en compte les besoins des collaborateurs, le Lean Management repose sur un ensemble de principes fondamentaux. Le premier principe consiste à mettre le client au cœur de l’entreprise tout en analysant la valeur ajoutée qui est définie par le client final en fonction du produit ou service qui satisfait son besoin. Le deuxième principe stipule que la chaîne de valeurs, concernant l’ensemble des actions par lesquelles passe un produit ou service avant d’être mis à la disposition du client final, doit être analysée. L’objectif étant d’identifier la non-valeur ajoutée qui correspond à toute action que le client n’est pas prêt à payer. Relevées grâce aux outils de diagnostic, ces actions sont considérées comme des gaspillages qui doivent être réduits au maximum. Selon le troisième principe les entreprises sont appelées à tendre les flux de leurs processus. Il s’agit d’une opération qui passe par la minimisation de l’encours afin de livrer son client plus rapidement. Grâce à cela, l’entreprise réalise des gains en termes de coûts de stockage qui sont généralement très lourds financièrement. Le quatrième principe est, quant à lui, axé autour des collaborateurs. Il consiste à mettre les salariés au centre de l’entreprise en les impliquant afin de profiter de l’intelligence collective. Condition sine qua non de la réussite de l’implantation du Lean Management. Le dernier principe stipule que les quatre principes précédents doivent être appliqués en permanence. L’objectif est de s’engager dans un processus d’amélioration continue qui correspond à l’évolution permanente des besoins des clients.
Qu’en est-il de la boite à outils ?
La réussite de la mise en place du Lean Management repose sur la communication, l’organisation et la motivation des collaborateurs. Pour ce faire, les managers disposent d'une palette d'instruments, de méthodes et de bonnes pratiques tels que les 5S, le management visuel et le SMED pour ne citer que ceux-ci. Visant à garantir la qualité et la productivité au poste de travail, la méthode japonaise des 5S a pour objectif d’améliorer les tâches effectuées dans les entreprises de manière continue. Elle consiste à réaliser les cinq opérations suivantes : Débarrasser (Seiri), Ranger (Seiton), Nettoyer (Seiso), Standardiser (Seiketsu), Discipliner (Shitsuke). Contribuant à la communication et à l’image de marque de la société, le management visuel permet de définir un environnement de travail qualitatif et ce, par le biais d’outils visuels. L’objectif est d’être le plus près possible de l’opérateur, faciliter la réactivité avec ce dernier et, par conséquent, proposer une aide à la prise de décision. Le tout en facilitant et simplifiant la définition des objectifs. Le Single Minute Exchange of Die (SMED) est une autre méthode mise à la disposition des managers. Celle-ci permet de réaliser un changement rapide de série afin de réduire les temps non productifs. Elle rend le système de production plus flexible pour répondre aux besoins d’optimisation des stocks et des tournées d’approvisionnement.