Alcatel Submarine Networks, 406 employés et 16 hectares dédiés à la fibre
Ça y est : le rachat d'Alcatel par Nokia est effectif. Mais subsiste une exception à Calais : ASN, pour Alcatel Submarine Networks, bien qu'il fasse partie du groupe Nokia, reste géré indépendamment, comme une entité séparée. L'occasion rêvée pour dresser le portrait de ce géant de la fibre optique sous-marine.
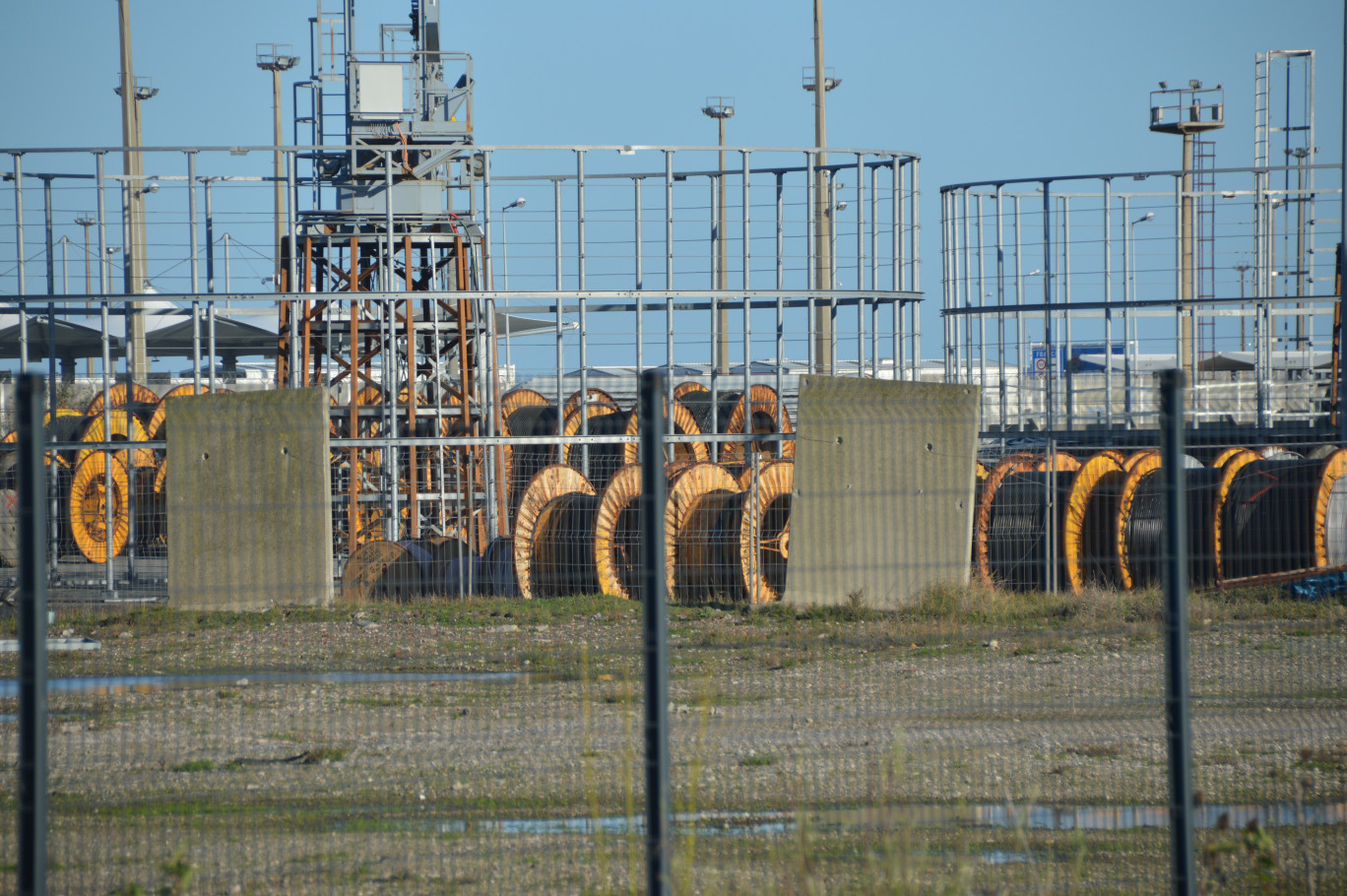
Fabrication, transport, pose… Sur le site calaisien d’Alcatel Submarine Networks, ce sont 45 000 km de fibre optique sous-marine qui sont posés tous les ans au fond des océans. Des câbles qui nécessitent une technique très particulière à chaque étape du processus. L’entreprise, où travaillent plus de 400 personnes (406 pour être précis, dont 7% de femmes et 8% de personnes en situation de handicap, et 60 employés dans la recherche et le développement), propose 95 métiers différents en son sein. L’usine de câbles a, selon sa directrice Patricia Boulanger, de grandes chances de rester indépendante après la fusion d’Alcatel-Lucent et de Nokia. «Alcatel-Lucent a décidé de continuer l’exploitation de ses activités de câbles sous-marins (ASN) en tant que filiale en propriété exclusive», publiait Alcatel-Lucent sous forme de communiqué, le 6 octobre dernier. Une bonne nouvelle au vu du savoir-faire déployé sur le site calaisien. Rappelons qu’Alcatel-Lucent voulait à l’origine trouver un repreneur pour l’exploitation de sa filière câble, décision sur laquelle le groupe est revenu.
D’autre part, l’actualité de l’entreprise est riche : entre le passage de Google sur le site calaisien, au mois d’octobre, pour discuter d’un projet en collaboration avec Intel en Amérique du Sud et le rachat par Nokia d’Alcatel-Lucent, à l’exception d’ASN, il n’y a pas de quoi s’ennuyer.
Preuve de l’importance du site calaisien, trois fonds d’investissements étaient en lice en juillet pour le rachat de la filière câblière d’Alcatel. En 2013, ASN (qui détient deux autres sites, un à Greenwich, au Royaume-Uni, et un à Trieste, en Italie, Calais étant la plus grande usine de câbles de fibre optique au monde, avec une production mensuelle moyenne de 3 500 km) aurait affiché un chiffre d’affaires de 400 millions d’euros.
De l’épaisseur d’un cheveu à la taille du poing. Car le savoir-faire déployé par l’usine calaisienne a quelque chose d’unique : depuis la fibre optique livrée à l’entreprise par grands rouleaux jusqu’à ces kilomètres de câble déployés sous les mers, il y a des dizaines d’opérations. Tout d’abord, il faut souder les fibres optiques pour que les câbles soient longs de 70 à 100 km selon la nature de la fibre – à chaque longueur de câble est posé un répéteur, prévu pour relancer le signal dans la fibre, afin qu’il ne s’épuise pas. Ensuite, c’est une coloration qui est posée sur cette fibre, afin de la reconnaître d’un bout à l’autre de la ligne. Les fibres – une douzaine par câble en général – sont glissées dans un tube en inox. À l’intérieur de la gaine d’inox, on coule une sorte de gel afin de protéger la fibre, de conférer une souplesse au câble et dans le but de protéger la fibre de l’hydrogène auquel elle est très sensible.
Autour de l’inox est tressé de l’acier pour maintenir une pression constante sur le câble. Autour, une gaine de cuivre est fixée, afin d’alimenter les fameux répéteurs en énergie. À l’intérieur, un polymère est coulé afin de couper une éventuelle infiltration d’eau. Le câblage est ensuite enveloppé dans une couche de polyéthylène, pour isoler électriquement le câblage en cuivre. L’ensemble est ensuite laissé tel quel pour tapisser les grands fonds marins, ou armé davantage s’il est destiné à être posé sur les côtes, pour le protéger des agressions (d’éventuelles morsures de poissons, par exemple). Ainsi, après avoir scruté les fonds dans lesquels seront posés les câbles, on leur applique une simple armure ou une double armure. Ce sont simplement des câbles en acier enroulés autour de la structure en polyéthylène. Pour une simple armure, il faut compter un jeu de câbles en acier, qui peut être doublé. Le tout est recouvert d’une dernière couche (du bitume) et prêt à être posé. Le câble double armure ainsi fabriqué peut supporter 80 tonnes avant de rompre.
Lean. «70% des salariés sont formés au lean manufacturing et sont certifiés», affirme Patricia Boulanger. Lorsqu’on fabrique des câbles, il est indispensable de procéder de cette manière. «On ne peut pas fabriquer de câbles à l’avance. Comme il existe différentes sortes de câbles pour différents reliefs sous-marins, il nous faut attendre le tracé exact du relief, et donc du câble pour le mettre en route…» Les contraintes sont nombreuses dans le secteur : on ne fabrique pas un câble comme on fabriquerait autre chose : la linéarité des câbles oblige littéralement ASN à fonctionner de manière linéaire.
Acheminement. Le travail de l’entreprise ne s’arrête pas là : une fois fabriqués, les kilomètres de câbles sont acheminés par un tunnel vers l’un des trois bateaux de pose que détient ASN, l’Île-de-Bréat, l’Île-de-Batz et L’Île-de-Sein. Là, les câbles sont stockés dans de grandes cuves cylindriques d’un diamètre de 19 mètres et hautes de 7 mètres, dans lesquelles ils sont enroulés. «La partie du câble arrivant en dernier est la première à sortir. Il faut être attentif à ça», sourit le jeune capitaine Philippe Kervella. L’homme de 34 ans, aux commandes du navire câblier, a la responsabilité d’une pose quasi millimétrée : «La trajectoire et la vitesse sont essentielles lorsqu’on pose un câble. Les câbles que l’on pose ne supportent pas la suspension.» Pour éviter la suspension, il est donc important de suivre exactement le tracé du relief sous-marin. Par grand fond, si le bateau s’arrête, l’opération tombe à l’eau… Le bateau doit donc parcourir 250 km par jour. Par opposition, par petit fond, le besoin de garder la tension du câble impose une vitesse minorée, de 20 km par jour.
Pour ce faire, Philippe Kervella est assisté d’un équipage de 45 à 70 personnes (aujourd’hui, l’équipage est composé d’une soixantaine d’hommes) qui chargent les câbles et opèrent les derniers tests sur les répéteurs. «Le plus gros du travail se fait à quai, affirme le capitaine. Entre les chargements de câbles, de vivres, la sécurité à assurer, il y a du travail…»
Diversification. Toutefois, ASN Calais ne fait pas que des câbles. L’entreprise a diversifié son offre, depuis la revalorisation d’anciens câbles téléphoniques sous-marins jusqu’au développement de capteurs sismiques pour l’extraction de pétrole – usage dédié aux productions pétrolières et gazières en mer. ASN propose bien plus que de la fabrication et de la pose de câbles.
La revalorisation est simple : les câbles usagés sont fendus dans la longueur pour récupérer le polyéthylène, puis les câbles de cuivre et d’acier restants sont désintégrés à l’aide d’un couteau et séparés par magnétisme. Ainsi, chaque partie des câbles usagés peut être revalorisée. Cet atelier de revalorisation a été primé en 2014.
D’autre part, le système de capteurs mis en place sur les poches de pétrole ou d’essence permet d’exploiter davantage ces réserves naturelles. De 35% d’une poche de pétrole, on peut avec ce système en extraire 50%. Le principe : le champ de capteurs posé sur la poche pétrolière émet un signal, récupère une réponse qui permet de quantifier le pétrole contenu. Le procédé permet aussi de détecter d’éventuelles failles sismiques dans les poches pétrolières, qui peuvent avoir des effets désastreux. Enfin, ASN possède quatre bateaux dédiés à la maintenance des 575 000 km de fibre optique d’ores et déjà posés au fond des océans.