Implantée à Houlle, près de Saint-Omer
3D-MétalPrint cultive le titane
Deux ans après son installation à Houlle, 3D-MétalPrint a trouvé un premier échelon de développement via un investissement conséquent et un savoir-faire qui ne cible que la complexité. La société vient de faire entrer deux machines depuis le début du printemps. Rencontre avec un jeune dirigeant, amoureux du titane...
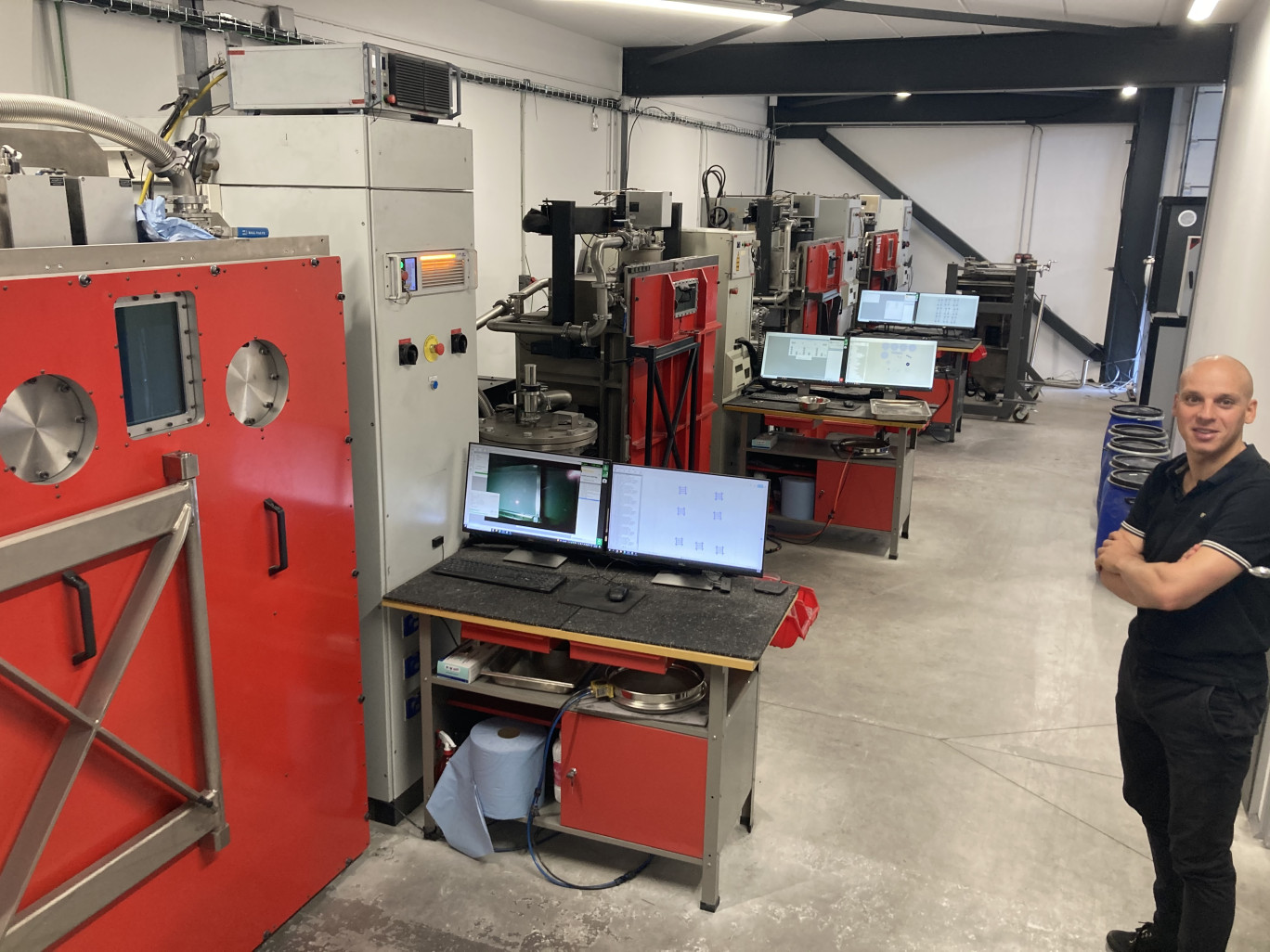
Imprimer du matériel spatial dédié à la conduite des ondes ; réaliser, avec un alliage de titane, des prothèses pour la chirurgie ; donner des formes complexes, aux propriétés variées, pour inscrire telle pièce dans un environnement médical, industriel ou aéronautique… Tels sont les trois piliers technologiques de la petite entreprise houlloise d’impression de métal 3D-MétalPrint. «Fabrication additive métallique à haute valeur ajoutée» pétitionne la documentation de l’entreprise de trois salariés et qui affiche plus d’un demi-million d’euros de chiffre d’affaires, huit ans après sa création. «J’ai travaillé dans le secteur médical après avoir étudié à l’Institut lillois d’ingénierie de la santé (ILIS)», raconte Maxime Hugues, 32 ans, fondateur et dirigeant de l’entreprise.
Une poudre aux propriétés presque liquides
L’activité se découpe par tiers égaux : le médical, l’industrie et l’aéronautique. «20% de notre activité part à l’export, en Grande-Bretagne, aux Pays-Bas et en Belgique. Au niveau local nous ne réalisons que 5% de notre chiffre d’affaires» précise le cadre qui a passé cinq ans dans l’hôtel d’entreprises de la Communauté d’Agglomération de Saint-Omer. Désormais installé dans des locaux plus spacieux, il rencontre tout de même des problèmes de place avec l’arrivée de deux machines, il y a deux mois.
Ce sont des imprimantes 3D façonnées pour imprimer du métal. Le process est délicat ; «Nous sommes sur la fusion d’une matière qui est poudreuse, mais qui a des propriétés quasiment liquides. Et qui, par fusion, devient solide dans cette chambre étanche» explique Maxime Hugues. C’est une production lente à l’échelle de la dizaine de microns. Ici, que du complexe et de la petite série. «Ce sont des pièces à très haute valeur ajoutée, difficiles à usiner, en tôlerie, en fonderie. Le matériau principal est le titane. Très résistant et à la fois flexible. Deux fois plus léger que l’acier, quasiment inoxydable, biocompatible (dans le médical), avec très peu de perte...» ajoute le dirigeant.
De la dentelle en titane
Sur une table contiguë au bureau, plusieurs pièces complexes aux formes alambiquées : un implant de hanche maillé pour laisser la place à la repousse de l’os, un petit bras articulé avec une double courbe... «De la dentelle. Ce que nous faisons, c’est transformer une matière en une seule étape. Avec un lit de poudre découpé au laser» sourit l’entrepreneur.
Avant ce résultat, dessinateurs, graphistes, ingénieurs et plusieurs batteries d’essais formeront les préparatifs au lancement de la production. Chaque pièce est confidentielle. Et peut coûter des milliers d’euros… Alliance de l’optique, de la mécanique, de l’électronique, du pneumatique (pour la chambre à vide) et de la chimie. «Chaque matière a sa couleur. Le titane bleuté, l’aluminium un peu jaune» pense tout haut le jeune homme. Dans l’atelier, trois méga-imprimantes travaillent. Deux autres font office de secours. Depuis sa création, l’entreprise est rentable. Et son dirigeant s’essaie à un autre usage du titane. La bijouterie...