Billy-Berclau : Atlantic installe un cobot dans son usine de production
Afin d’augmenter la productivité d’une ligne de production de pompes à chaleur dans son usine de Billy-Berclau, mais aussi et surtout améliorer le quotidien des opérateurs, le Groupe Atlantic a sollicité l’expertise de la société Lilloise JL Corp quant à l’installation d’un cobot UR10 d’Universal Robots.
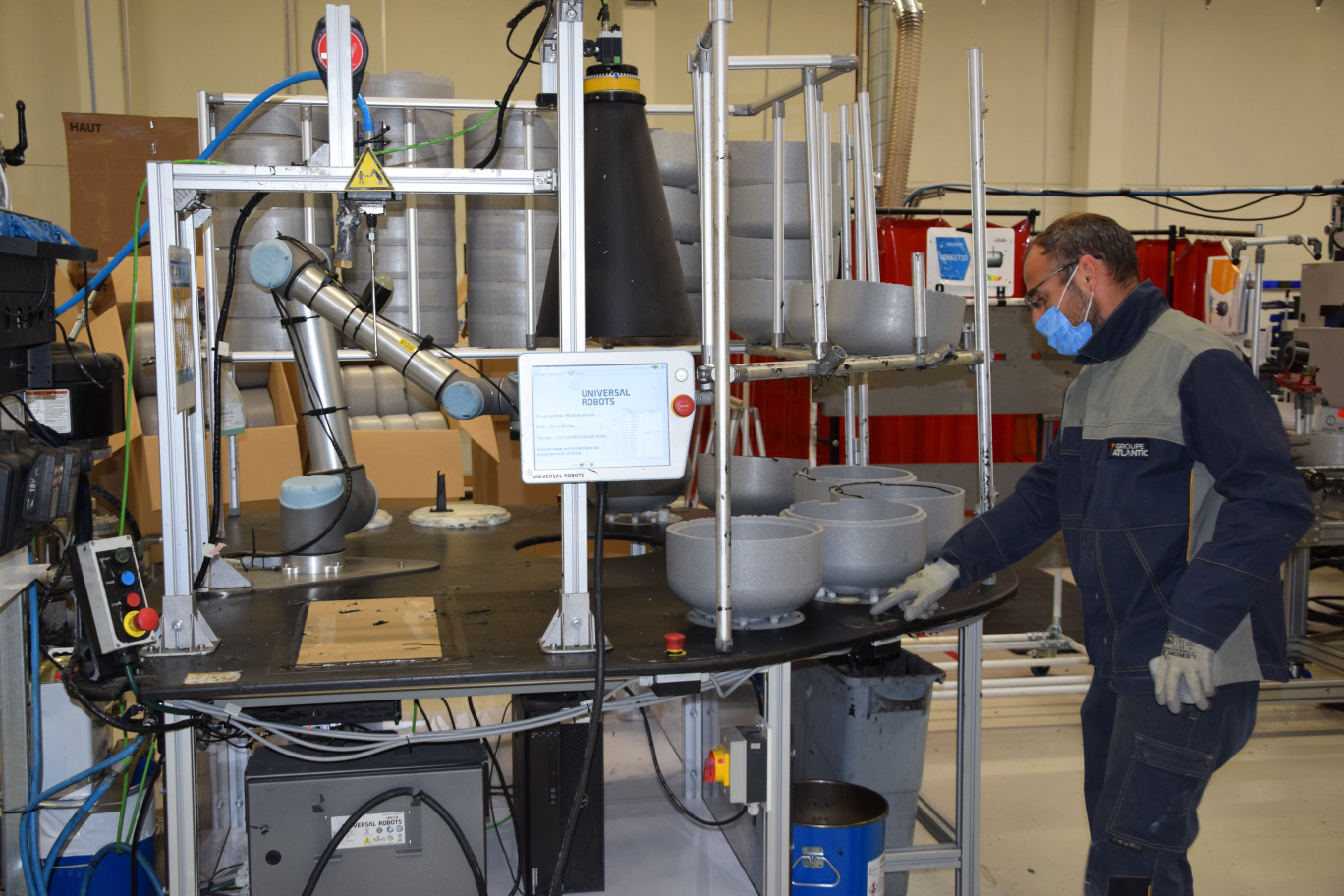
Ce deuxième site en région a ouvert en février 2016 sur 23 000 m2, en parallèle de l’usine historique de Merville, pour satisfaire à la production de chaudières murales gaz. Alors qu’une extension de 1 600 m2 dédiée aux métiers de l’emboutissage est en cours, l’usine de production de Billy-Berclau emploie à ce jour 400 salariés pour une production annuelle de 80 000 unités par an et 120 000 modules pour pompe à chaleur.
Une solution développée par JL Corp
Face à l’augmentation de l’activité, le Groupe Atlantic souhaitait améliorer la productivité sur un poste d’encollage des coques d’isolation de cuve en inox pour ses pompes à chaleur et diminuer la pénibilité du travail de ses opérateurs sur ce poste. Les opérateurs étaient en effet sujets à des troubles musculo-squelettiques, devant effectuer les mêmes gestes jusqu’à 200 fois par jour et tenant à bout de bras un lourd pistolet à colle. Le mastic utilisé, naturellement noir et collant, posait également des problèmes de propreté.
Pour l’accompagner dans ce projet, l’entreprise s’est orientée vers l’intégrateur certifié Universal Robots sur les Hauts-de-France, la société JL Corp. Basée à Lille, celle-ci est spécialisé dans les études, la conception industrielle et l’intégration de robots collaboratifs pour les entreprises de différents secteurs comme l’industrie automobile, l’industrie pharmaceutique, la mécanique ou encore la plasturgie. Gage de son savoir-faire, au-delà de ses 30 années d’expérience, elle a reçu l'Award du meilleur CSI d'Universal Robots en France pour 2020.

Bien-être et productivité
Pour répondre aux besoins de son client, JL Corp a élaboré une solution cobotique (dispositif robotique conçu pour interagir avec un humain, contrairement à un robot classique) capable de suivre l’augmentation de volume demandée par le site, tout en étant compacte et sécurisée. L’installation est complètement autonome, puisque le cobot se saisit des coques pour opérer un contrôle qualité puis les encoller, et totalement sécurisée. Son implantation n’a donc pas demandé une réorganisation de la production.
En cas de problème, comme une rupture de colle ou la chute d’une pièce, le cobot alerte les opérateurs qui viennent le résoudre et relancent le cycle. Et la satisfaction est aujourd’hui au rendez-vous puisque l’installation a permis d’améliorer le bien-être des opérateurs, une valeur majeure revendiquée par la direction de l’usine, et d’augmenter la productivité de plus de 50% sur cette activité. En parallèle, la consommation de colle a diminué de près de 40%. Que demander de plus ?