De 160 000 à 240 000 tonnes de fil de cuivre par an
Lens : le groupe Nexans investit 90 M€ dans une nouvelle usine
Améliorer les conditions de travail, augmenter la capacité de production et renforcer le recyclage du cuivre, tels sont les objectifs de l’investissement de 90 M€ annoncé par le groupe Nexans sur son site de Lens. Rencontre avec Maxime Debay, directeur de l’usine régionale.

L’usine lensoise est aujourd’hui la seule fonderie de cuivre pur en France. Concrètement, la fonderie sort des barres de 8 millimètres affinées jusqu’à 0,2 millimètres dans l’atelier de tréfilage, des câbles qui sont ensuite embobinés sur des tourets. Les fils de cuivre de Nexans électrifient aussi bien les bâtiments que les voitures et les avions, et sont destinés aux projets haute-tension acheminant l'électricité entre villes et pays, notamment pour la fabrication de câbles sous-marins. «70% de notre production est destinée aux entités du groupe» précise le directeur du site depuis septembre 2023.
30% de matière première recyclée
La nouvelle usine de 8 000 m2 (la surface globale du site est de 68 000 m2, ndlr) abritera une ligne de production automatisée, des équipements dotés des dernières technologies et un nouveau four à fusion de 30 mètres de hauteur. «Hors activités de haute tension, c’est un investissement record pour le groupe Nexans ! Avec cette nouvelle usine qui remplacera l’actuelle d’ici deux ans, la production annuelle du site passera de 160 000 à 240 000 tonnes, la priorité étant de continuer à alimenter les usines Nexans en fil de cuivre, notamment les usines italiennes du groupe. C’est donc pour nous une responsabilité supplémentaire !»
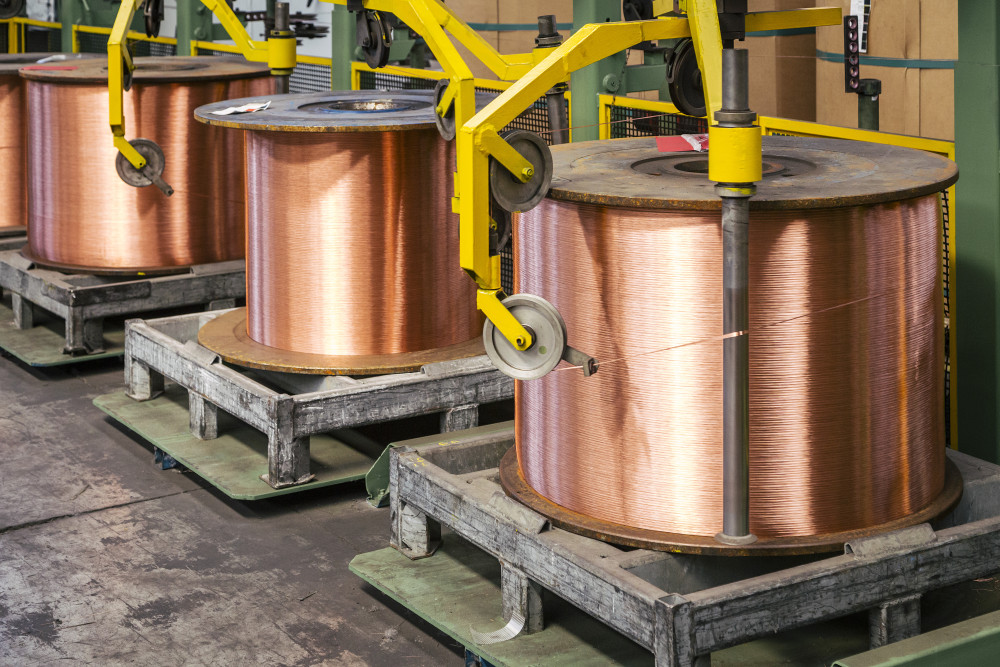
Et Maxime Debay de poursuivre : «Sur ces 240 000 tonnes, 30% seront fabriquées à partir de cuivre recyclé. Dès 2030, les capacités d’extraction minière ne devraient plus être suffisantes pour couvrir la demande mondiale, nous devons donc être en capacité de recycler beaucoup plus ! Et pour être cohérente avec notre politique environnementale, la nouvelle usine permettra de réduire le volume d’eau nécessaire au refroidissement du cuivre et des panneaux photovoltaïques seront installés en toiture. Enfin, au-delà de la productivité et des enjeux environnementaux, l’objectif de cet investissement de 90 M€ est aussi et surtout d’offrir de meilleures conditions de travail à nos collaborateurs. L’écrémage (décrassage de la surface après fusion, ndlr) se fait aujourd’hui manuellement, demain cette étape sera réalisée par un robot ».
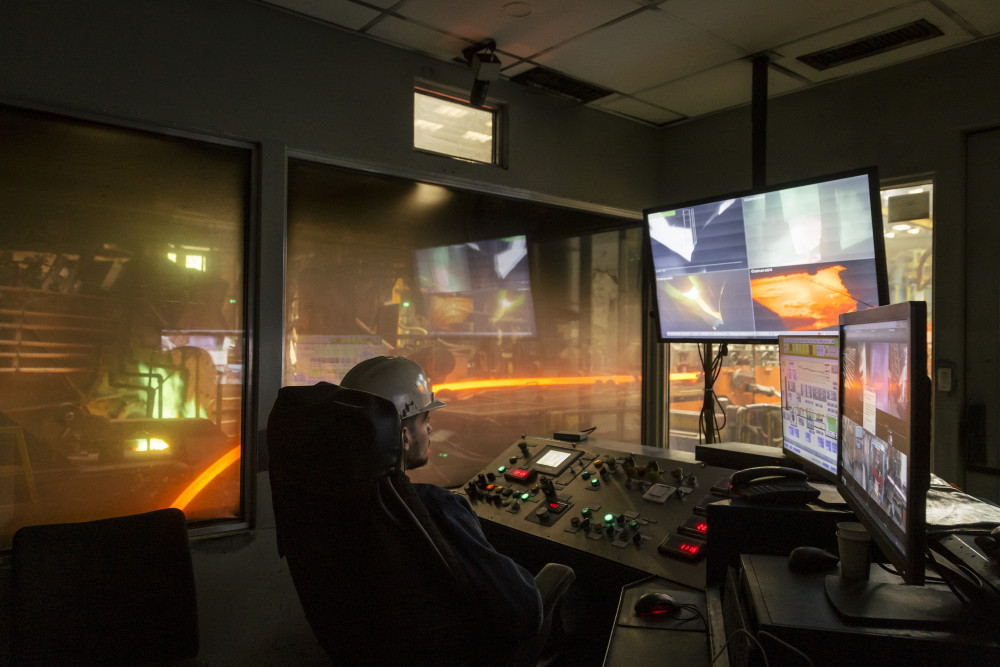
Démarrage de la production en octobre 2026
Une nouvelle stratégie qui implique une refonte du modèle organisationnel de l’usine. «A terme, nous recevrons 80 000 tonnes de déchets par an, soit une vingtaine de camions supplémentaires par jour pour atteindre un flux quotidien d’environ 80 camions… Nous avons besoin de place ! Le bâtiment qui abrite la coulée deviendra donc une zone de stockage» précise-t-il. «L’objectif est de s’appuyer sur notre réseau pour récupérer les déchets et nous approvisionner auprès des centres de tri. Tout l’enjeu réside ensuite dans l’affinage – la séparation entre le cuivre et les autres métaux – pour arriver à un cuivre pur, de qualité équivalente à notre production non issue de matière première recyclée, grâce à une technologie appelée FRHC et développée par un industriel Italien».
Si les travaux de création de bassins enterrés sont en cours, la construction de la nouvelle usine devrait démarrer en février prochain, pour un démarrage des process de production en octobre 2026. «Le challenge des deux prochaines années est de construire la nouvelle usine, tout en maintenant la production».
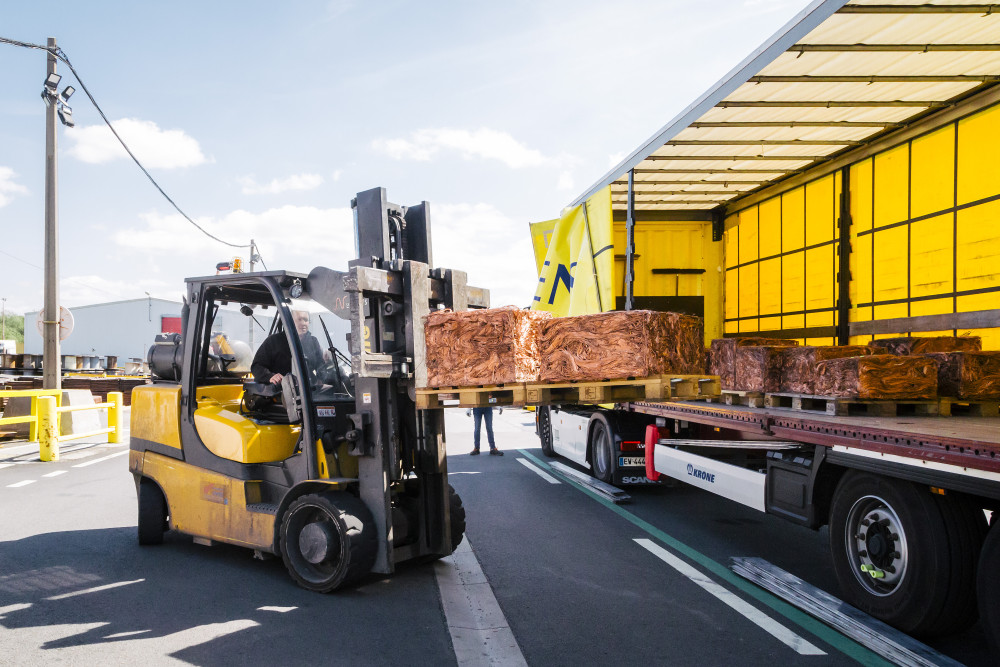
Une usine fondée en 1855 !
L’histoire débute il y a 169 ans avec l’ouverture d’une usine de fabrication de cordes en chanvre. Entièrement détruite au cours de la première guerre mondiale, l’usine est reconstruite pour démarrer la production de câbles en acier qui serviront, notamment, à la fabrication du pont de Tancarville à la fin des années 1950. En 1921, ses dirigeants ouvrent le premier atelier de tréfilage de métal (étiré en fil) pour la production de câbles électriques et se dotent en 1970 d’une fonderie de cuivre.
Désormais, le site de Lens est l’un des maillons forts du groupe Nexans. La production de câbles en acier a été abandonnée au profit de la production de conducteurs en cuivre : une bobine de 5 tonnes sort de l’usine toutes les 8 minutes, soit 700 tonnes par jour (de quoi électrifier un paquebot de croisière) et 160 000 tonnes par an, pour 160 salariés.
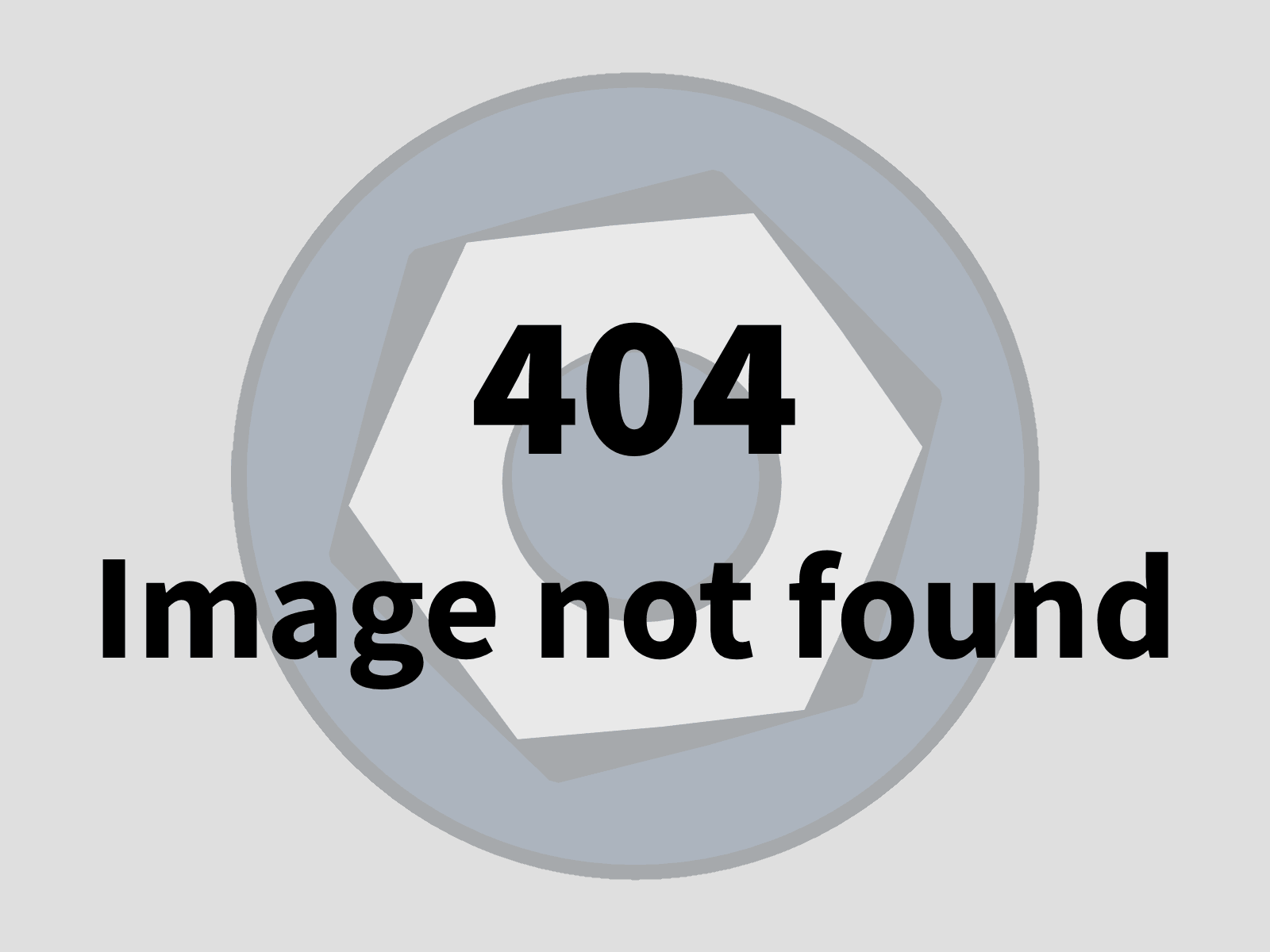